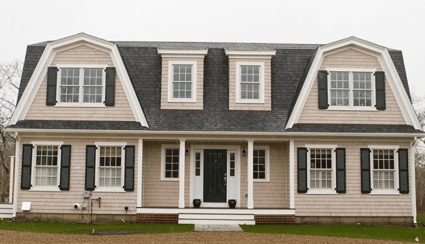
On Martha’s Vineyard, style and price are par for the course. For builder Bill Potter, he saw opportunity to deliver both, with modular, at the right time at the right price.
According to MV Times, when the markets crashed back in 2008, Potter and his wife Terry started asking themselves what they could do with the company then known as Potter Construction.
That brainstorming turned into Squash Meadow, the couple’s firm combining modular construction with onsite building practices, known as hybrid prefab. This would allow higher end customers on Martha’s Vineyard to custom design their homes at an attractive price in what was a skittish economy.
With the concept in mind, the Potters were ready to begin. Then the challenges began.
“But we needed a modular building partner who was willing to work with us, to change their business practices to accommodate the need of clients here,” said Bill Potter.
“We made a list of seven modular construction companies in the Northeast and pitched them all on their notion. Six said no, but Westchester Modular Homes in Wingdale, N.Y., on the New York/Connecticut border, said yes.”
The two companies married their visions, and started on what would turn into a fruitful journey.
“We’d been doing some green building, and we wanted to continue doing that, as well as offering more design choices, and Westchester was willing to adapt,” said Potter.
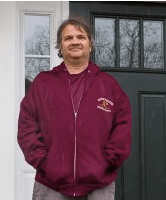
Originally, Potter Construction had four employees and would hire crews when they were awarded a building contract.
Since their move to hybrid construction, the company, now known as Squash Meadow, now has a management team of ten, and Potter says that on any given day you’ll see “50 Island guys working at our work sites.”
Potter says that the hybrid model proof is in the pudding: clients see savings of 20 percent over traditional site built homes and three month completion times versus one year. For client Julie Fay and her family, they are believers.
“This was a stellar experience for us. We bought our land last June, and we were fully moved in by September. Their computerized design system let us walk through every room [in the design phase] and see what our choices looked like. We got a realistic view down to appliances and interior details,” said Fay.
“We wanted a green design, and we had a contractor friend look over our shoulders every step of the way. Squash Meadow could do anything. Of course some choices involved a price tag, but it was an easy and predictable process.”
A View from the Architectural Angle
Phil Regan, managing partner of Vineyard Haven based Hutker Architects Inc., provided his take on modular.
“The modular industry is an affordable option and historically a sort of bucket of parts in dimensions of two, four and eight feet built in units small enough to be shipped. There has not been a lot of design but that is changing,” said Regan.
“Modulars are not quite small houses now, but generally are under 2,000 square feet. Above that level, design plays a larger role. There is market demand for modular design but it seems to me that onsite construction and modular methods right now are like a pair of magnets — drawn to each other but when they get close, the direction starts to shift.”
An Expert Take
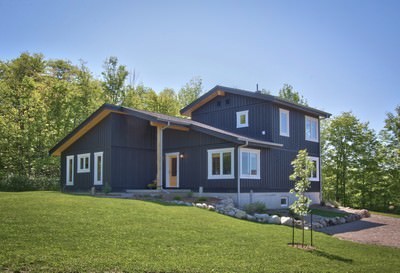
In MHProNews’ popular, in depth interview series, “A Cup of Coffee with...” Hybrid Prefab Homes President Otis Orsburn shares important details about this.
“The hybrid prefab home methodology has been readily accepted by traditional construction contractors, investors, lenders and the ultimate homeowner, ” said Orsburn.
“Another success is creating and managing the plan set that addresses the entire vertical construction of the home.” Orsburn stated that, “Historically, this has been the largest dysfunction when building a home that is replete with factory-built nuances that traditional contractors have not dealt with before.”
Orsburn continued.
“These nuances are viewed as weaknesses because they haven’t been utilized in mainstream construction. After attending my classes for general contractors, these contractors become our spokes people.”
For more on activities on bringing affordable housing options to Martha’s Vineyard, including “tiny homes,” click here. ##
(Image credits are as shown above, and when provided by third parties, are shared under fair use guidelines.)

Submitted by RC Williams to the Daily Business News for MHProNews